What do you get if you combine the talents of two Quebec companies – one specializing in pharmaceutical research into cannabinoide-derived drugs and the other in producing acoustic panels for interior decoration?
The answer might surprise you: Quebec’s first producer of much-sought-after N95 face masks for frontline medical workers.
That’s what happened when teams from Tetra Bio-Pharma and Artofix joined forces in an unusual alliance in the fight against COVID-19.
It all started last month, when Guy Chamberland, CEO and Chief Regulatory Officer at Tetra Bio-Pharma, saw a Facebook post about another Quebec-based company that had decided to launch itself into the war against the pandemic by converting part of its production line to produce the N95 face masks.
That company was the Longueuil-based Artofix, which specializes in producing 3D acoustic panels to cover walls and ceilings in offices and large indoor open-space areas.
‘Our contribution to society’
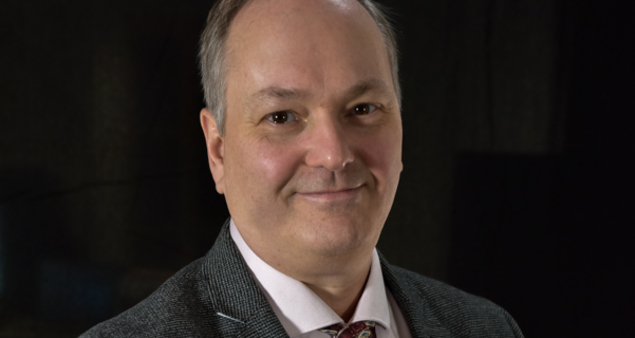
Guy Chamberland is the CEO and Chief Regulatory Officer at Tetra Bio-Pharma, which specializes in research into cannabinoide-derived drugs. (Submitted by Tetra Bio-Pharma)
Chamberland said like many people in his industry he wanted to jump into the battle against COVID-19 and help find solutions.
“We realized rapidly that they certainly didn’t have the expertise we do in getting through Health Canada [certification process], or the U.S. Food and Drug Administration,” Chamberland told Radio Canada International in a phone interview.
Tetra Bio-Pharma had already reached out to another company that had decided to convert a part of its production capacity to produce hard surface disinfectants and Chamberland knew they could help Artofix too.
Chamberland contacted Artofix general manager Jason Duval to offer him his help clearing the regulatory hurdles completely free of charge and without any preconditions.
“It costs a lot actually to go through the regulatory process if you don’t have that expertise internally,” Chamberland said. “For us it was kind of our contribution to society.”
Tetra Bio-Pharma helped Artofix set up its quality assurance system and the regulatory team worked all night to prepare the application for a Medical Device Establishment License (MDEL) for a Class 1 medical device manufacturer, Chamberland said.
“They were just so motivated that they just did it,” Chamberland said. “It was fun to see how everybody jumped in to help the others and maintain our own work.”
An urgent need
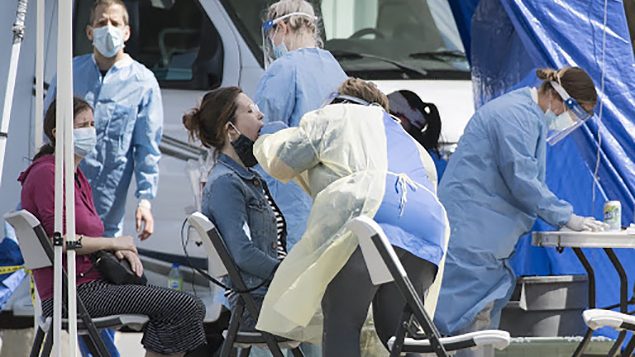
A woman is tested for COVID-19 at a mobile clinic in the Montreal neighbourhood of Saint-Michel, Sunday, May 3, 2020, as the COVID-19 pandemic continues in Canada and around the world. (Graham Hughes/THE CANADIAN PRESS)
Duval said the idea of converting part of the business to produce masks came to him when the virus started wreaking havoc in Canada and stories of shortages of masks and personal protective equipment dominated the headlines.
Artofix’s parent company, Duvaltex, specializes in producing textiles for the furniture industry and for medical applications.
“We know textiles and we’re very good at molding 3D textile shapes,” Duval told Radio Canada International. “We started designing a 3D model of the mask and then we started looking at filtration materials.”
It was important for the company to use innovative ways of creating the new mask to avoid using the usual raw materials for the production of N95 masks that were already in very short supply due to the increased demand, Duval said.
“We knew we could make a very comfortable 3D molding of a mask and that’s what we did,” Duval said.
The design team worked almost non-stop for the first few weeks to come up with the design of the mask, he said.
The company built a prototype and found the right raw materials to build it, and had the prototype undergo a battery of tests at a laboratory at the University of Concordia, Duval said.
“Once we knew we had something, we started redesigning our equipment for production, we started procuring the raw materials and also to be able to sell the mask into the healthcare system, we had to get our medical device establishment licence,” Duval said.
This was where they partnered with Tetra Bio-Pharma.
“They really helped us along the way,” Duval said. “It’s a licence that normally takes months to get and we did it very fast by having a very good training by them and also adapting our equipment and technology.”
Quebec’s first N95 mask
Artofix’s development team has been able to create an adjustable one-size-fits-all hermetically sealed mask, Duval said.
The company is working with Health Canada to get the mask tested and certified for use in the healthcare system in Canada, he said.
The certificate could be approved “any day now,” Duval said.
“We are very advanced in the process,” he added.
Artofix is also working on getting certification by the U.S. National Institute for Occupational Safety and Health (NIOSH), which would allow it to access the American market as well.
“We think it’s very important to be able to manufacture these products locally in Canada,” Duval said. “And I think we can have a very good competitive mask for the long-term.”
Artofix repurposed some of its existing technology to produce the shell of the mask, but the company is looking into designing a fully automated production line to cut down on costs but also to mitigate the risks of infection among workers on the assembly line, Duval said.
The company thinks it will have to hire 30 additional employees to ramp up the production of masks once it clears all the regulatory hurdles, he said.
“We have a capacity of about 200,000 masks per week if we run 24/7, that’s only for our facility in Longueuil, and we’re looking at another facility that we have near Quebec City, in Beauce,” Duval said.
A lesson for governments
The federal government is looking to purchase 300 million masks to deal with the pandemic and replenish its rapidly dwindling reserve stocks as it prepares for the second wave, Duval said.
“I think it’s very clear that they don’t want to see another shortage of protective equipment,” Duval said. “That’s something nobody wants to see again.”
Duval said they are confident they can produce the mask at a competitive pricing.
Most of the raw materials for the mask are produced in Quebec and in other parts of Canada, Duval said.
Chamberland said the scramble to procure personal protective equipment during the pandemic should serve as a lesson to the federal government that it must maintain some critical manufacturing capacity in Canada.
Canada’s ability to produce generic drugs has been hollowed out by companies moving their production to places like China and India because they can produce there at a cheaper price, he said.
“To save a few pennies we actually destroyed an essential business that we needed in the time of crisis,” Chamberland said. “That for me is a major lesson that I hope the government will learn.”
For reasons beyond our control, and for an undetermined period of time, our comment section is now closed. However, our social networks remain open to your contributions.